Detail Design Case Study
- Emily Spooner
- Feb 18, 2023
- 4 min read
Updated: May 10, 2023
PRECEDENT 1- Louis Vuitton Metal Screen-
(Maison Louis Vuitton des Champs-Elysées in Paris)

In 2005 this metal screens were installed in Louis Vuittons flagship store in Paris to entice customers on a journey around the store through each department. They allowed the store to be sectioned into departments while still giving glances of the next section to entice customers further into the store. The screen is made up of 100,000 individual elements and has a combined surface area of 1000 m2.
Materials
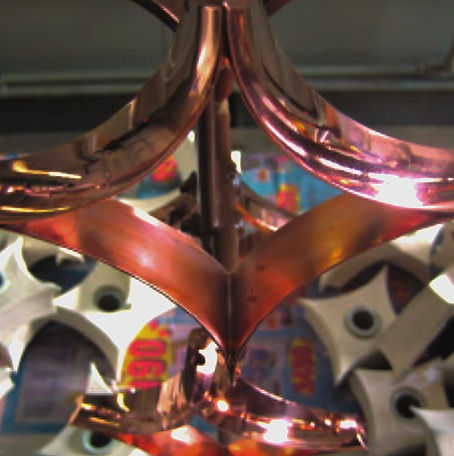
Pressurised Aluminium-
The main section of the screen is made up of circular ornaments made of out pressurised aluminium that when put together allude to the well known pattern seen in LV's fasion and accessory ranges. Some of the circular elements are filled with Intarsia to replicate the LV logo that is spread sporadically throughout the circles. The aluminium is then coated in a variety of metals including copper, nickel and silver. Then topped with a protective coating.
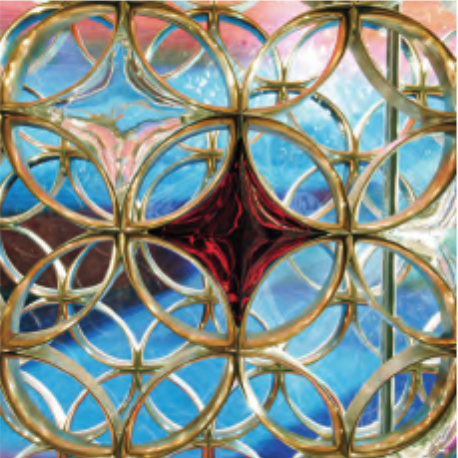
Intarsia-
The intarsia is used to create the inserts of the screen which are added during the final stages of the manufacturing process. They are a symbol of the high standard of handcrafts that go into Louis Vuittons products. The coloured glass, wood and other materials used are of the highest standards to again represent the quality of their products and materials.

Other Materials-
While the central screen is made of purely metal the materials that surround the screen in the accompanying displays complement the companies ethics and dedication to handcrafted techniques. They include leather, wood, porcelain and coloured glass, all of which align themselves with the luxury couture brand and high end finish their products represent.
Design Development
The initial concept was derived from the Louis Vuitton flagship store in Tokyo in 2003 and has since become a staple in their store designs.
Initially the feature was just a design element that referenced the classic trade mark logo of LV, but has been refined to provide other purposes within the store. For example the screen is also used to filter sunlight from the windows of the store as well as providing some privacy to the customers to make their experience feel more luxurious.

The screens pattern can be linked directly to Louis Vuitton's signature fabric shown above. The technical drawings to the left show how the elements fit together to create a strong element that can be manipulate to create arches and curves dependent on the size and location of the store.
PRECEDENT 2- Aoba-tei -
(French Restaurant in Sendai)

The restaurant was constructed in 2005 over a
7 month period in an existing building covering a 2 story space. The effect the building is known for is accomplished using a collection of perforated steel panels at different thicknesses and varied lighting levels creating images of Japanese Zelkovas (a Japanese oak tree typical of the Sendai area). The screens flow around the restaurant while the service zones are concealed to the rear of the building. It is considered to be a high end dining experience.

Design Development
The original drawings of the building show how the trees are spread out on the curved walls. This pattern was then converted to holes that vary in diameter to allow the light to make these shapes in both the panels and the shadows created. By having low levels of lighting besides the panels it creates an ambient lighting experience.
Construction
The digitalised photo was created with numerically controlled perforations of 4, 6 and 9 mm diameter at spacings of 15 mm. Light installations are placed behind the steel panel wall in the cavity to the existing walling and illuminate the perforations in varying intensities. The play of light and shade in the foliage of the real trees on the street is thus drawn into the interior of the building.
My Response

In response to the Aoba-Tei restaurant design I developed these root drawings using varying sizes of circles. I feel that this concept is very successful and would have a similar affect as the precedent if lit correctly with either natural light creating shadows or back lit with artificial light in a darker setting.
PRECEDENT 3- Growth
(Expanding Origami Pot - Design Council Spark)
This company aims to create products that can be reused at the point they would normally be discarded and end up in landfill. Their main product is the expanding plant pot that is shown in the video below, it is designed to grow with the plant in 3 steps as it unfolds using the basic principles origami in a complex construction process. The concept mimics that of natural growth where plants expand over time and blossom into new growth.
Exploring Origami
Origami is an ancient art that is normally associated with paper craft but is increasingly applied to architecture and product design in its appearance. However it is rare that the movement that is associated with origami is used within design. This product relies solely on these movements and while on appearance it is a simple design the mechanical workings of the product are extremely intricate and complex.
My Response
I really enjoy the geometry that origami can bring to both drawings and structures the model I made used a single sheet of paper to create an intricate cylindrical object. It only requires a handful of fold and creases non of which are complex but the end result is geometrically complex. If I was to try and create this shape using another construction method it would be hard to do.
References-
Schittich, C. (Ed.). (2008). Interior surfaces and materials : Aesthetics, technology, implementation. Walter de Gruyter GmbH. (https://ebookcentral.proquest.com/lib/portsmouth-ebooks/reader.action?docID=3045429) P.g. 98-101, 134-137
Comments